Reconstruction background
With the development of modern industrial technology, automated processing has become the mainstream of contemporary industry. Good structural performance has become an important indicator of the product, and the milling head is the core accessory of the milling and boring machine products. At the beginning of 2015, due to the fact that the piston rod and the pusher bar of the CNC gantry machining center attached to the right-angle milling head clamping tool cannot be effectively reset, the automatic right-angle milling head of the accessory is unreliable and cannot be fully utilized. The role of the attachment right angle milling head in automated machining. Under this circumstance, the design institute set up a group of “Clamping knife resetting of the right angle milling head of CNC gantry boring and milling machine.†The team members measured the site and completed the renovation project.
2. Status analysis
The loose-knife structure of the right-angle milling head of the CNC gantry machining center produced by our company is a hydraulic loose-knife, and the broach structure is tensioned by the disc spring (see Figure 1). Attachment right angle milling head automatic loose knife structure shown in Figure 2. When the knife is loosened, the piston rod protrudes under the action of the pressure oil, and after the contact with the pusher rod, the disc spring force is moved forward to realize the automatic loosening knife. When the knife is clamped, the piston rod is moved to the left by the pusher bar under the action of the disc spring. In order to avoid the two still in contact after the position, the spring reset and pneumatic cylinder reset technology are adopted, but the effect is not good in practical application. Stable, cylinder thrust and spring return force do not overcome the hydraulic return resistance and the friction of the seal on the piston rod. The consequence is that the spindle rotates when the piston rod and the push rod are not disengaged, resulting in the piston rod. Rubbing against the contact surface of the pusher bar and grinding together.
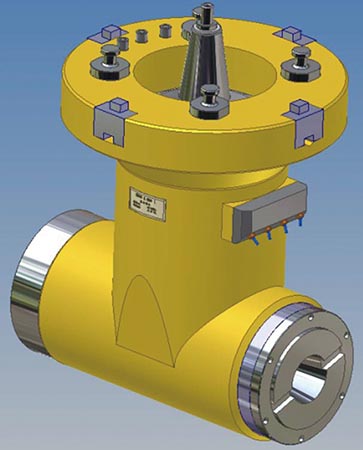
figure 1
figure 2
3. Determine the transformation goals
When the right angle milling head is clamped, the piston rod and the push rod are reliably separated, and the modification is completed accordingly.
4. Analyze the main factors leading to this phenomenon
The panel members analyzed the influencing factors of the attachment of the right angle milling heads at the processing site as shown in the attached table.
Before implementing the retrofit, it is necessary to find out the cause of the high back pressure. After many trials, discussions and analysis, the main reasons are as follows:
(1) CNC gantry machining center is a heavy-duty machine tool. The height of the machine tool is large, and the oil in the oil pipe will generate a large pressure under the action of gravity.
(2) The pipeline of the entire hydraulic system passes through a plurality of drag chains, and the pressure loss of the pipeline is greatly caused by the towline being bent and long.
(3) The valve block on the headstock is installed on the same substrate, and the oil return is realized through a pipeline, and the oil return of each valve group affects each other.
5. Implementation plan
For the above reasons, we have adopted the corresponding transformation plan:
(1) Configure an independent oil return line to open the valve block of the right angle milling head of the right angle milling head and other valve components to avoid mutual influence.
(2) Bold the return line to reduce the return pressure loss.
(3) Optimize the arrangement of the pipelines in the towline.
(4) Add a layer of spring inside the return spring to increase the spring return force.
(5) When clamping the knife, the PLC program is delayed by 3~4s, so that the hydraulic cylinder pipeline has sufficient time to remove the pressure.
6. Transformation results
After the test, the back pressure of the oil return line of the right angle milling head of the accessory is reduced from 0.6MPa to about 0.1MPa, and the piston rod and the pusher rod end face are reliably separated, and the 2mm gap required by the production pattern technology is achieved. This transformation was carried out on multiple CNC gantry machining center accessory milling heads, and the transformation effect was good.
references:
[1] Wang Wei. Mechanical Design Standard Application Manual [M]. 2 Volume. Beijing: Mechanical Industry Press, 1997.
[2] Zhang Yu, Liu Ping. Geometrical Tolerance and Measurement Technology [M]. Shenyang: Northeastern University Press, 1999.
[3] Kong Qinghua, Liu Chuanshao. The Foundation of Extreme Coordination and Measurement Technology [M]. Shanghai: Tongji University Press, 2002.
[4] Zhao Mingsheng. Mechanical Engineer's Handbook [M]. Beijing: Mechanical Industry Press, 2005.
[5] Zhang Haiwei. Analysis of Dynamic Performance of CNC Machine Tools and Its Structural Optimization[J]. Manufacturing Technology and Machine Tools, 2006: 58-61.
[6] Mechanical Design Manual Joint Writing Group. Mechanical Design Handbook [M]. Beijing: Chemical Industry Press, 2008.
[7] Wang Xinrong, Chen Yongbo. Fundamental of finite element method and ANSYS application[M]. Beijing: Science Press, 2008:131-185.
[8] Wu Zongze. Mechanical Structure Design [M]. Beijing: Science Press, 2010.
When out and about or walking to and from school, the Children Safety Vest is the accessory for children to be seen in. Garments are available for ages from 3-4 to 11+. We ensures that the wearer will be outstanding in day and night. All items are manufactured to EN1150 and are CE marked. You can order our existing style of safety vest, but also, they can be customized.
Children Safety Vest
Children Safety Vest,Child Safety Vest,Led Safety Vest,Safety Waistcoat
Xinxiang Zhongke Reflective Material Co., Ltd. , https://www.safetyvest.pl